۹۰ درصد ریختهگری در کشور به روش پیوسته است
تولید رقابتی فولاد با روش ریختهگری مداوم
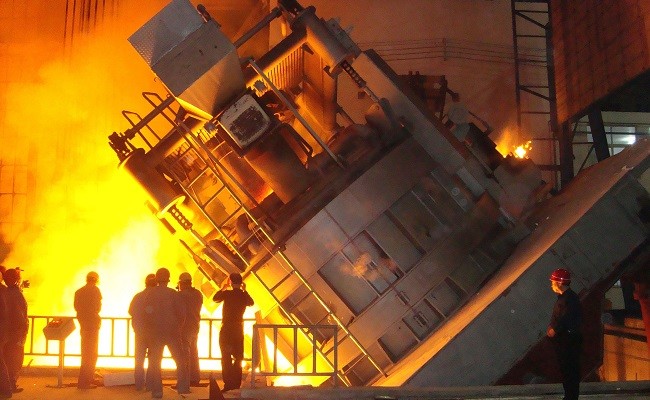
دو نوع مختلف ریختهگری مداوم یا پیوسته و ریختهگری غیرمداوم در ذوب مواد معدنی در دنیا وجود دارد. هر کدام از این روشها علاوه بر اینکه مزایا و معایب خاص خود را دارند محصولات متفاوتی هم تولید میکنند.
به گزارش استیل تریدر، در بین ۲ روش ذکر شده آنچه در ایران عمومیت دارد استفاده از روش غیرمداوم است که حدود ۹۰ درصد ریخته گری در واحدهای ذوب چه در فولادسازیها و چه مس یا فروآلیاژها به این روش و ۱۰ درصد به روش ریخته گری مداوم انجام میشود و شاید علت این امر به خاطر نامحدود بودن میزان تولید محصولاتی باشد که با این روش غیرمداوم انجام میشود برخلاف روش مستقیم که نمیتوان هرگونه کالایی را با این روش تولید کرد.
ریخته گری پیوسته
در روش ریختهگری پیوسته، فلز مذاب بر اساس یک فرآیند پیوسته، به جامد تبدیل میشود و شامل چندین فرآیند مهم است. این فرآیندها موثرترین راه برای جامد کردن حجم زیادی از فلز و تبدیل آنها به اشکال ساده برای پردازشهای بعدی هستند. در جهان بیشتر فلزات پایه شامل بیش از ۵۰۰ میلیون تن فولاد، ۲۰ میلیون تن آلومینیوم و یک میلیون تن مس، نیکل و... با استفاده از فرآیند ریخته گری پیوسته به تولید انبوه میرسند. این روش نسبت به دیگر فرآیندهای ریختهگری، هزینه سرمایه گذاری بالاتر اما هزینه اجرایی کمتری دارد.
این فرآیند پربازده ترین روش چه از لحاظ هزینه و چه از لحاظ انرژی برای تولید انبوه قطعات فلزی نیمه تمام با کیفیتی سازگار با انواع ابعاد و شکلها به شمار میآید. سطح مقطع قطعات میتواند مستطیلی، برای نورد بعدی و تبدیل آن به ورق یا صفحه، مربع یا دایره برای محصولات طویل، و حتی اشکال «استخوان سگی» برای نورد و تبدیل به تیرهای « H »یا « L» باشد.
روش ریختهگری مورد استفاده در ایران
رییس تولید ناحیه فولاد سازی سبا متعلق به فولاد مبارکه درباره روشهای مختلف ریختهگری میگوید: به طور کلی ۲ روش برای ریختهگری وجود دارد که این روشها شامل روش ریخته گری تختال ضخیم یا غیرمستقیم و ریخته گری تختال نازک یا مستقیم است. محمود محمدی فشارکی بیان میکند: روش غیرمستقیم در کارخانههایی مانند فولاد مبارکه مورد استفاده قرار میگیرد که در این روش تختالهایی به ضخامت ۲۰۰ میلیمتر تولید میشود و بعد اسلبها انبار شده و کنترل کیفی روی آنها انجام میشود و پس از بررسیهای لازم به مرحله بعدی رفته و به نورد تبدیل میشوند که به آن روش تختال ضخیم هم گفته میشود.
وی میافزاید: در روش ریختهگری تختال نازک یا مستقیم که درکارخانه فولاد سبا انجام میشود ورقهایی تا ضخامت ۵۰ میلیمتر تولید میشود که ابتدا به کوره پیش گرم رفته و بعد تبدیل به نورد میشوند. وی درباره روشی که در ایران بیشتر استفاده میشود، خاطرنشان میکند: در کشور ما حدود ۹۰ درصد محصولات ورق به روش ریختهگری غیرمستقیم یا ضخیم و ۱۰ درصد به روش مستقیم یا تختال نازک تولید میشود. محمدی فشارکی عنوان میکند: هر کدام از روشها مزایا و معایب خاص خود را دارند ازجمله اینکه در روش ریختهگری نازک بسیاری از محصولاتی که بین ۰/۰۷ تا ۰/۱۵ کربن داشته باشند را نمیتوان تولید کرد زیرا دچار ترک خوردگی میشوند.
وی خاطرنشان میکند: از سوی دیگر روش مستقیم مزیتهایی مانند مصرف انرژی، نیرویانسانی و هزینههای سرمایهگذاری کمتر دارد اما مهم ترین عیب آن محدودیت در تولید انواع محصولات است. رییس تولید ناحیه سبا در فولاد مبارکه اظهار میکند: در روش تختال ضخیم یا غیرمستقیم هزینههای سرمایهگذاری و تجهیزات بسیار زیاد است چراکه محصولات تولیدی باید دارای ضخامت ۲۰۰ میلیمتری باشد که این مسئله نیازمند تجهیزات و نیروی انسانی و سرمایهگذاریهای زیادی است بنابراین تولید این کالاها درجه حرارتی زیادی میخواهد. اما مزیت این روش در محصولات فراوانی است که میتوان تولید کرد.
وی درباره اینکه در دنیا بیشتر از چه روشهای استفاده میشود، بیان کرد: در دنیا هر ۲ روش ریختهگری مورد استفاده قرار میگیرد چراکه در روشهای مختلف پیوسته و غیرپیوسته محصولات متفاوتی تولید میشود به همین دلیل نیاز است در کشور هر ۲ روش مورد استفاده قرار گیرد اما در روش غیرمستقیم هزینهها به ویژه در مصرف انرژی بالا و در روش مستقیم هزینهها پایینتر است.
وی خاطرنشان میکند: در روش تختال ضخیم ورقهای کمکربن، متوسط کربن و پرکربن تولید میشود که مربوط به فولادهای ساختمانی میشوند روشهای تختال نازک هم فولادهای ساختمانی هستند اما بیشتر برای پروفیلهای در و پنجره مورد استفاده قرار میگیرند. بیشتر فولادهایی که در ایران تولید میشودند، ساختمانی است. محمدی فشارکی عنوان میکند: این مزیت در ریختهگری پیوسته یا ورقهای نازک وجود دارد که در آن فناوریهای جدید مورد استفاده قرار میگیرد و در این روش برخی از مراحل ذوب حذف میشود.
روش مداوم در کارخانههای دولتی
حجتالله ابراهیمزاده، مدیر کارخانه فولاد جنوب میگوید: به طور کلی ۳ نوع ریختهگری وجود دارد یکی ریختهگری قطعه است که از قدیم این روش بهکار میرفته و قطعات ماشینآلات به این روش تهیه میشد که با روی کار آمدن ذوبآهن اصفهان ریختهگری مداوم هم بهکار گرفته شد، با فولاد خوزستان گسترش پیدا کرده و با فولاد مبارکه تقویت شد. از سال ۸۲ نیز بخشهای خصوصی به حوزه تولید فولادی وارد شدند و روش دیگری به عنوان روش اینگاس یا غیرمداوم را اضافه کردند.
وی میافزاید: بیشترین حجم تولید فولاد کشور مربوط به ریخته گری مداوم میشود که فولاد خوزستان با سالانه ۳ میلیون تن، فولاد مبارکه ۴/۵ میلیون تن و فولاد هرمزگان و بیشتر کارخانههای دولتی از روش ریختهگری مداوم برای تولید شمش استفاده میکنند. مدیر کارخانه فولاد جنوب عنوان میکند: ریختهگری اینگاس درکارخانههای کوچک و برای تولید شمشهای ۳ متری به کار میرود که از روش قالبریزی استفاده میکنند. در طول یکسال کل تولیدات این مجموعهها به یک میلیون تن هم نمیرسد اما قطعه ریزی در بخشهای خصوصی و دولتی همچنان ادامه دارد.
به گفته وی، عمده تولید فولاد یعنی۹۰ درصد بهوسیله ریختهگری مداوم انجام میشود که از این میزان هم ۹۵ درصد در دست بخش دولتی است و از روش غیرمداوم بیشتر بخشهای خصوصی استفاده میکنند. ابراهیم زاده درباره اینکه قیمت تمام شده در کدام روش پایینتر است، بیان میکند: قیمت تمام شده در بخش تولید شمش در روش قطعه ریزی پایینتر است اما در تولید محصول استفاده از روش قالبی یا اینگاس قیمت تمام شده پایینتر است ولی کیفیت شمش در روش مداوم بالاتر است و به همان نسبت از قیمت تمام شده بالاتری هم برخوردار است. بنابراین شمش تولیدی در روش اینگاس با روش مداوم اختلاف قیمت دارند که هزینه تمام شده در روش مداوم هم بیشتر از روش اینگاس است.
وی تاکید میکند: در سایر کشورها هم بیشتر روش پیوسته را مورد استفاده قرار میدهند البته روش تولید فولاد در ایران به نسبت کشورهای پیشرفته کاملا متفاوت است. بهطور مثال ژاپن برای کشتیسازی فولاد تولید میکند به همین دلیل روش قطعه ریزی بیشتر مورد توجه است. چین هم تا ۸۰ درصد تولیدات فولاد خود از روش مداوم استفاده میکند همچنین هندوستان ۴۰ درصد از روش اینگاس و ۶۰ درصد از روش مداوم استفاده میکند.
وی ادامه میدهد: اگرچه هزینه سرمایهگذاری اولیه در ریختهگری مداوم بالاتر از روشهای دیگر است و انرژی بیشتری نیز تولید میکند اما این روش تنها روشی است که برای تولید شمش به کار میرود ضمن اینکه در ریختهگری مداوم امکان بالابردن ظرفیت تولید و به تبع کاهش قیمت تمام شده با سرشکن شدن هزینههای تولید بر میزان فولاد تولیدی وجود دارد و این تنها راهی است که امکان رقابت فولاد ایران را با سایر فولادهای تولیدی کشورهای دیگر را فراهم میکند.
- بهناز صفری-
استیل تریدر | مرجع خبر و تحلیل صنعت فولاد ایران وجهان